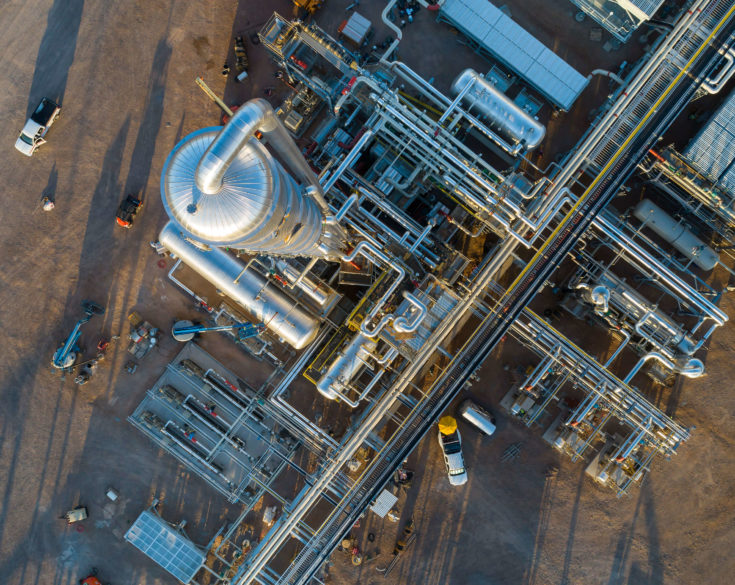
—
Industry Overview
Our experience in the gas processing and treatment industry includes a variety of treating, processing, utility, control, and electrical systems. We offer turnkey EPC support as well as focused services to start your venture or help you maintain existing assets in your energy portfolio. Our tailored solutions include:
- Opportunity identification
- Establishment of design criteria and constraints
- Estimating support and project budgeting
- Engineering and construction
- Brownfield design and retrofit
- Asset integrity management
- Technical inspections
- Maintenance
- Relocation and refurbishment projects
- Disassembly and relocation
Our execution strategy allows us to complete projects seamlessly. With each project, we aim to over-deliver, surpass our goals, and finish on budget and on schedule. 95 percent of our work is executed by our very own employees, which reduces shared cost and supply chain risk, and coordination with multiple contractors.
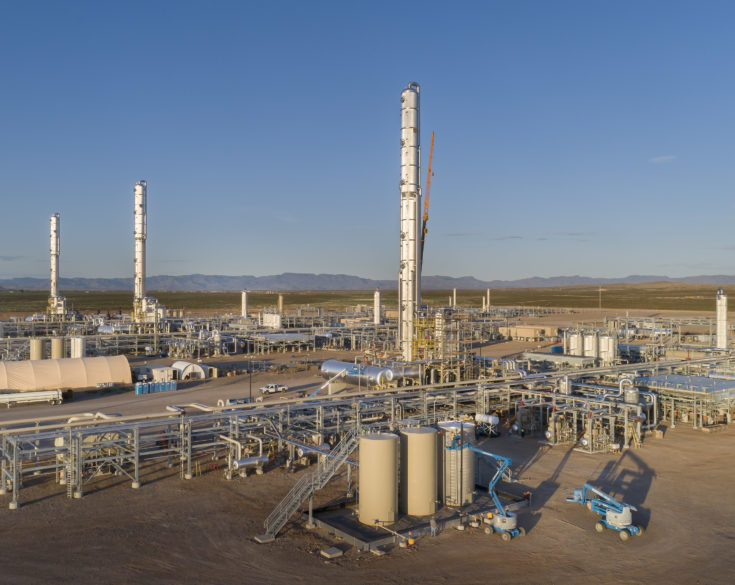
—
CRYOGENIC GAS PLANTS
Saulsbury is one of the leading EPC contractors in the gas processing industry. Since 2006, we have contracted 58 cryogenic processing facilities throughout the U.S. and across a variety of climates. These 58 cryogenic plants represent over 10 billion cubic feet per day of total base rated processing capacity.
Our extensive experience in the design/integration and installation of cryogenic gas plants spans various sizes, from 35-MMSCFD up to 230-MMSCFD single-train capacities, and technologies (GSP, RSV, SRX), as well as multi-train design and installations. Furthermore, Saulsbury has successfully executed cryogenic plant projects involving plant re-locations, brownfield plant upgrades/debottlenecking, and GSP-to-RSV conversion kits. Our experience likewise extends to the design and installation of all critical balance of plant major and utility equipment requirements to ensure a complete system is provided for necessary operation.
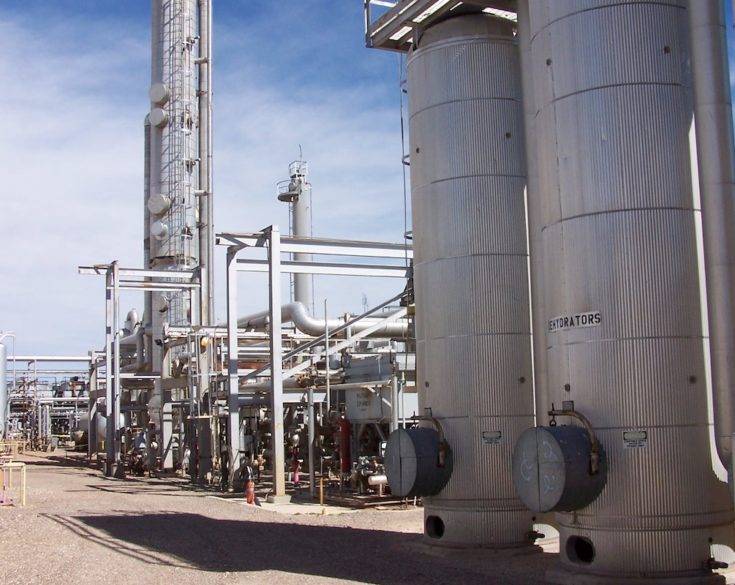
—
Dehydration
Our extensive experience in the specification, design/integration, and construction of dehydration systems spans numerous sizes, configurations, types (liquid desiccant vs. solid desiccant), and geographic locations. Saulsbury has installed over 100 dehydration and regeneration systems ranging from standalone small triethylene glycol (TEG) field dehydration units at field gathering compressor stations, in-plant molecular sieve dehydration systems capable of removing moisture content to trace levels and combinations thereof. Our experience likewise extends to the design and installation of all balance of plant utility and equipment requirements to ensure a complete system is provided for necessary operation.
Because of Saulsbury’s numerous relationships with equipment packagers and wide-ranging experience in the design and integration of various dehydration packages, we provide our customers with optimized solutions.
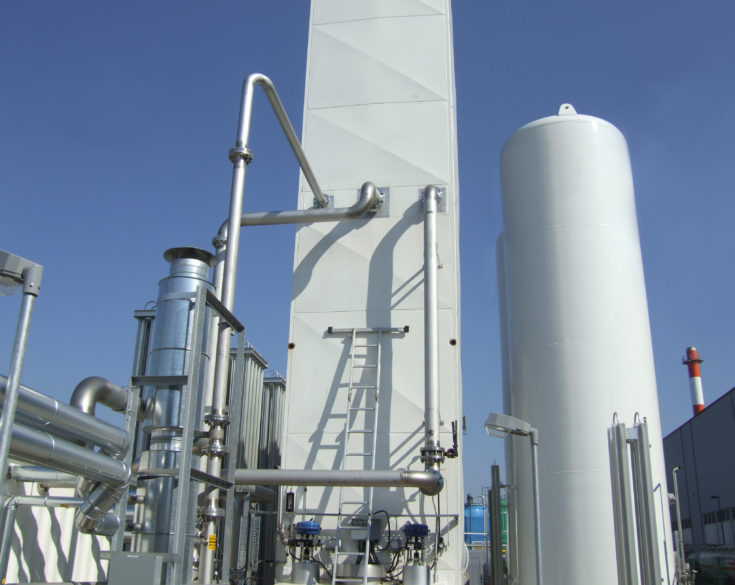
—
Nitrogen Rejection Units
Saulsbury’s vast experience includes the design, optimization, and/or integration of various unit operations in gas processing facilities, including the integration and installation of nitrogen rejection units (NRU). When a customer’s project requires the NRU process, Saulsbury has the expertise to partner with NRU package suppliers and provide the optimal sizing basis, balance of plant engineering/integration, procurement, and installation. We have extensive NRU experience and have completed multiple projects of varying sizes related to nitrogen rejection.
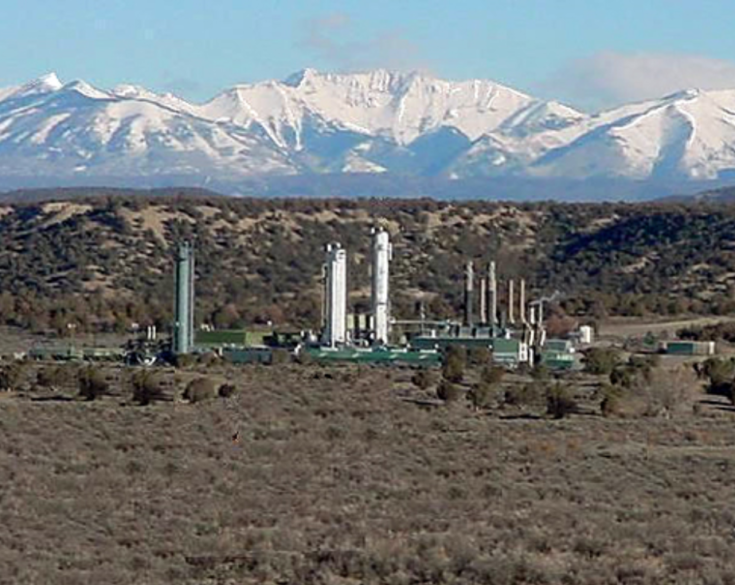
—
Amine
Our extensive experience in amine treating and regeneration specification, design/integration, and construction spans numerous sizes, configurations, services (gas vs. NGL), footprints, and geographic locations. Saulsbury has installed more than 75 amine treating and regeneration systems varying from small 15-GPM field treaters up to large 1,800-GPM in-plant treaters capable of removing large amounts of CO2 and H2S in the plant natural gas inlet streams. Our experience likewise extends to the design and installation of all balance of plant utility and equipment requirements to ensure a complete system is provided for necessary operation.
Because of Saulsbury’s numerous relationships with equipment packagers and wide-ranging experience in the design and integration of amine treating packages, we provide our customers with optimized solutions for their gas or liquid treating that are tailored specifically for the project’s requirements.
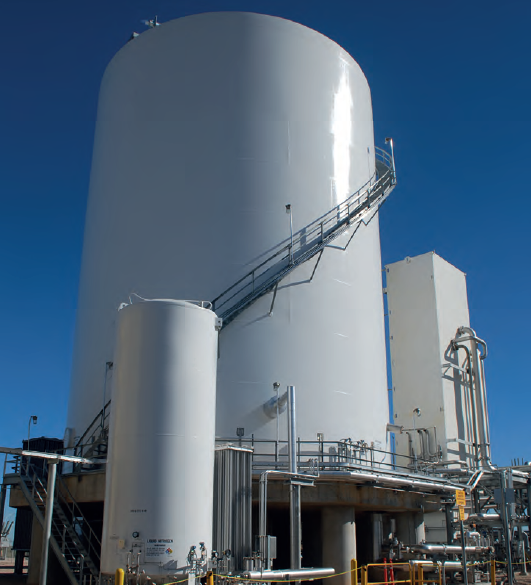
—
Air Separation Units
Working closely with technology providers for Air Separation Units (ASU) and gas processing plants, Saulsbury can support balance of plant engineering/design and all field construction. Our people have strong knowledge of the unique challenges with the construction and field assembly of cold boxes, plate-fin heat exchangers, turboexpanders, compression, and all associated equipment to support the ASU and specialty gas markets. Our experience includes hydrogen plants, oxygen plants, HyCO and syngas, helium, nitrogen, argon, and medical/specialty gases.
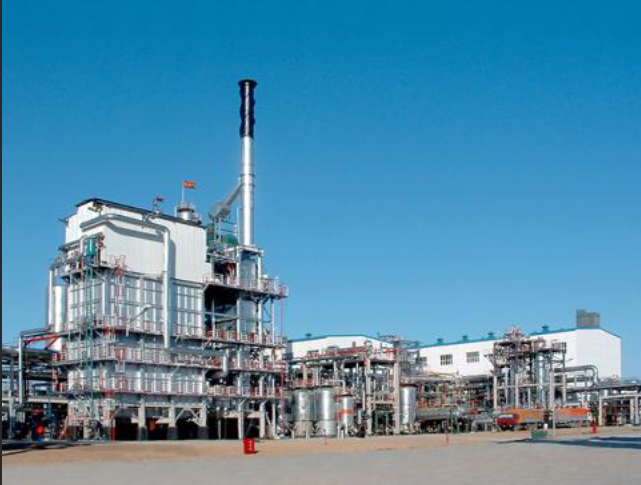
—
Ammonia Plants
Saulsbury and our key resources have experience in ammonia-related projects to support the fertilizer and specialty chemical markets. Much of our project experience involves working with world-leading technology providers for the successful feasibility and front-end engineering project development to later offer EPC solutions for the entire project delivery. As a U.S. leader in industrial markets, Saulsbury has expertise and experience to meet the challenges associated with the ammonia-related projects. Our experienced personnel has worked on liquid and gas-related ammonia projects for the industrial specialty markets as well as the liquid and solid fertilizer plants to support our U.S. agricultural clients.
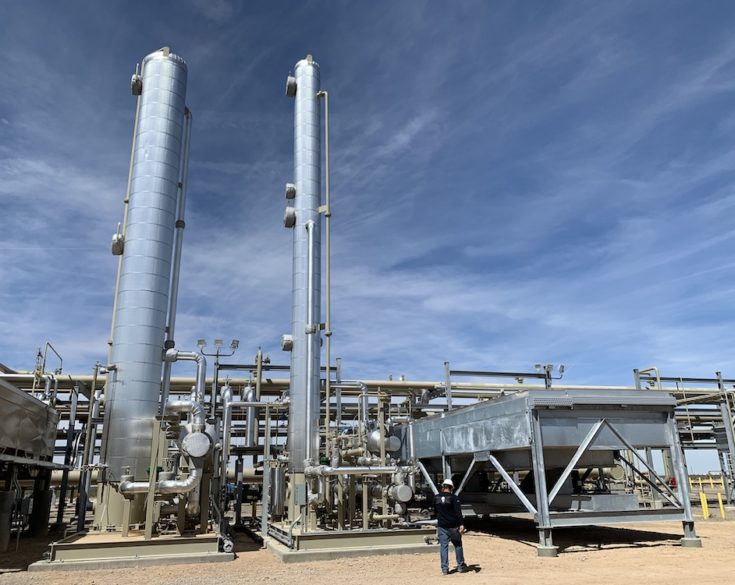
—
Condensate Stabilization
Condensate stabilization is a key unit operation for the handling and processing of pipeline hydrocarbon condensate that is captured and separated from natural gas that is received from incoming transmission pipelines. Separation of the liquid condensate from the incoming natural gas is critical to ensure proper operation and safety of downstream natural gas treating and processing equipment. Likewise, further processing and stabilization of this separated condensate are necessary in order to transform these raw pipeline liquids into marketable products that can be sold under specific product specifications by removing solids, free water, light hydrocarbons, carbon dioxide, and other impurities via filtration, separation, and distillation.
Our extensive experience in condensate stabilization specification, design/integration, and construction spans numerous sizes, configurations, resultant products (single-product vs. multi-product), footprints, and geographic locations. Saulsbury has installed over 40 condensate stabilization systems ranging from 1,000 bbl/day to 20,000 bbl/day in capacity. Our experience likewise extends to the design and installation of all balance of plant utility and equipment requirements to ensure a complete system is provided for necessary operation.
Because of Saulsbury’s numerous relationships with equipment packagers and wide-ranging experience in the design and integration of condensate stabilization packages, we provide our customers with optimized solutions that are tailored specifically for the project’s requirements, product specifications, and product takeaway options.